The fire pump is divided into different types according to different classification methods. It is widely sealed, leak-free and corrosion-resistant. It is widely used in environmental protection, water treatment, fire fighting, and other departments to pump all kinds of liquids. It is the ideal pump and fire protection system for creating leak-free, pollution-free civilized workshops and civilized factories. The pump types are similar, except that the head and flow are different. The selection criteria of the fire pump should be considered in five aspects according to the process flow and water supply and drainage requirements. The performance and technical conditions of the fire pump comply with the requirements of the “Fire Pump Performance and Test Methods” standard.
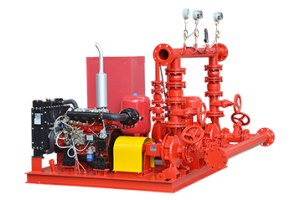
XBC6-25-IS end suction fire fighting package set
The efficiency of the fire pump is mainly determined by the three efficiencies of machinery, volume, and hydraulic power. Specifically, the main factors affecting the working efficiency of the fire pump can be divided into the following types:
- The efficiency of the fire pump itself is the most fundamental impact. For fire pumps under the same working conditions, the efficiency may differ by more than 15%.
- The operating condition of the fire pump is lower than the rated working condition of the fire pump, and the fire pump has low efficiency and high energy consumption.
- Motor efficiency remains essentially unchanged during operation. Therefore, it is important to choose a high-efficiency motor.
- The impact of mechanical efficiency is primarily related to design and manufacturing quality. After the fire pump is selected, the post management impact is small.
- Hydraulic losses include hydraulic friction and local resistance losses. After the fire pump is operated for a certain period of time, the surface of the impeller and the vane and the like are inevitably worn, the hydraulic loss is increased, and the hydraulic efficiency is lowered.
- The volume loss of the fire pump is also called leakage loss, including three leakage losses of the impeller seal ring, the interstage, and the axial force balance mechanism. The volumetric efficiency is not only related to design and manufacturing, but also related to post management. After the fire pump is continuously operated for a certain period of time, the gap is increased due to friction between the components, and the volumetric efficiency is lowered.
- The fire pump is evacuated and idling due to blockage of the filter cylinder, intake of the pipeline.
- Before starting the fire pump, the employees do not pay attention to the preparation work. The basic operating procedures such as the warm fire pump, the disk fire pump and the infusion fire pump are not completely implemented, which often causes the cavitation phenomenon of the fire pump, causing the fire pump to be noisy. Large vibration and low fire pump efficiency.